Mold polishing can be divided into a variety of processes, the use of different processing methods in silicone mold, in which the following surface treatment methods for the common process!
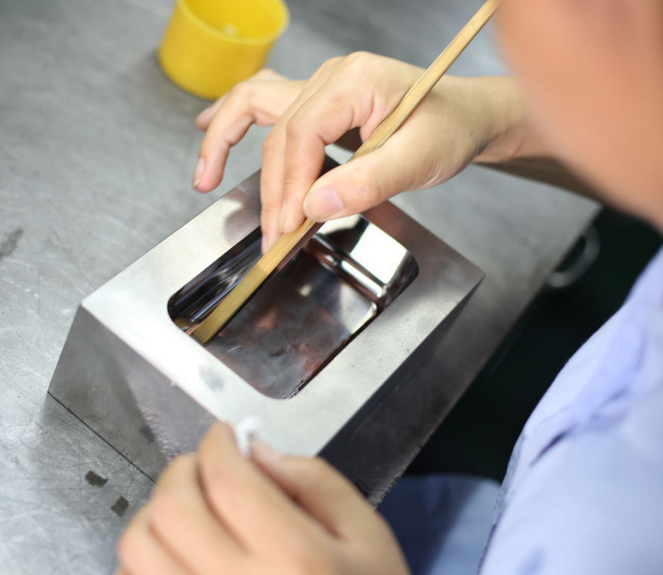
Electrolytic polishing:
Electrolytic polishing is based on the selective dissolution of the material surface of the tiny convex part of the surface smooth. Compared with chemical polishing, you can eliminate the impact of the cathode reaction, the effect is better. Electrochemical polishing process is divided into two steps:
(1) macroscopically leveled lysate diffusion into the electrolyte, the geometric roughness of the material surface decreased, Ra> 1μm.
(2) Low-level flat anode polarization, surface brightness increased, Ra <1μm.
Mechanical polishing:
Mechanical polishing is based on the plastic deformation of the cutting surface to remove the polished convex and get a smooth surface polishing method, the general use of stone, wool wheel, sandpaper, etc., mainly to manual operation, special parts such as the surface of the rotor can be used Turntable and other auxiliary tools, surface quality requirements can be super-precision polishing method. Ultra-precision polishing is the use of special abrasive, grinding fluid containing abrasive polishing press on the workpiece surface, for high-speed rotary motion. The surface roughness Ra0.008μm can be achieved by this technique, which is the highest among the various polishing methods.
Ultrasonic polishing:
Ultrasonic polishing is the use of ultrasound as a motivation to promote the fine abrasive particles to the workpiece surface at an extremely high speed, forcing the abrasive on the machined surface, thereby reducing the surface roughness of the polishing method.
Fluid Polishing:
Fluid polishing is to rely on the high-speed flow of liquid and abrasive particles scour the surface of the workpiece to achieve the purpose of polishing. Common methods are: abrasive spray processing, liquid jet processing, fluid power grinding and so on. Hydrodynamic grinding is driven hydraulically, allowing the abrasive medium to flow back and forth through the workpiece surface at high speeds. The medium is mainly made of special compounds that flow well at lower pressure and mixed with abrasive, and the abrasive can be silicon carbide powder.
Magnetic grinding and polishing:
Magnetic polishing is the use of magnetic abrasive in the magnetic field to form abrasive brush, the workpiece grinding. This method of processing efficiency, good quality, easy processing conditions, good working conditions. With a suitable abrasive, the surface roughness can reach Ra0.1μm.
Silicone products manufacturers in terms of mold polishing finish depends on the quality of the appearance of the product, so the same polishing process is an important process, and other industries polishing process is relatively speaking, mold polishing is to improve the processing efficiency of silicone rubber products and Product quality, etc., so you buy a good surface finish silicone products is precisely the mold polishing process is doing good!